Maximizing Efficiency with Machine Label Applicators
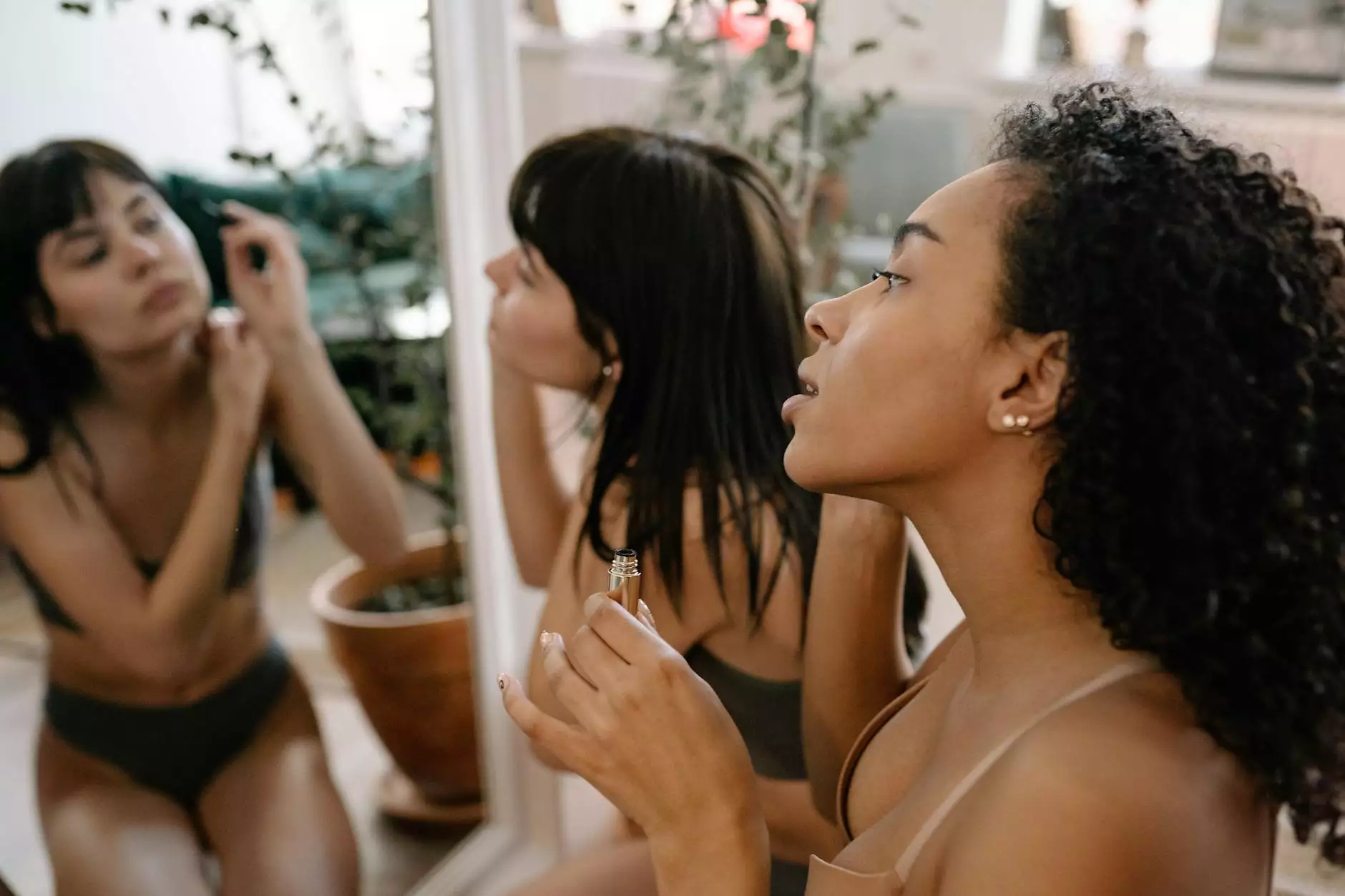
In today’s fast-paced business environment, efficiency and accuracy are critical for success. As industries strive for greater productivity, the demand for automation solutions has surged. Among these solutions, the machine label applicator stands out, particularly for businesses involved in printing services, electronics, and computer manufacturing.
What is a Machine Label Applicator?
A machine label applicator is an automated device designed to apply labels to products with high precision and speed. These machines range in complexity from simple handheld devices to advanced automated systems that integrate seamlessly into production lines.
Key Features of Machine Label Applicators
- Efficiency: Machine label applicators can label hundreds of products per hour, drastically reducing manual labor time.
- Consistency: They ensure that every label is applied in the same manner, maintaining product quality.
- Flexibility: Many machines can handle various sizes and types of labels, adapting to different product specifications.
- Integration: These machines can often be integrated with existing production lines for enhanced workflow.
Benefits of Using Machine Label Applicators
Incorporating a machine label applicator into your business operations offers a myriad of benefits that can enhance overall productivity and accuracy.
1. Increased Productivity
With the ability to consistently apply labels at a much faster rate than manual labeling, businesses can significantly improve their output. This increase in productivity allows for more products to be labeled and shipped in a shorter time frame, directly impacting profitability.
2. Cost-Effectiveness
While there is an initial investment in acquiring a machine label applicator, the long-term savings are substantial. Reduced labor costs, minimal mistakes, and less product waste lead to a quicker return on investment.
3. Enhanced Product Quality
Labels are crucial for conveying important information about products. A botched label can lead to compliance issues or customer dissatisfaction. The precision of a machine label applicator ensures that all labels are correctly applied and accurately positioned, significantly minimizing errors.
4. Improved Safety
Automating the labeling process reduces the risk of workplace injuries associated with repetitive tasks. Employees can focus on more strategic roles while machines handle the more dangerous environments of high-volume product labeling.
Types of Machine Label Applicators
Choosing the right machine label applicator depends on several factors including the type of products, labeling speed needs, and production line setup. Here are the most common types:
1. Manual Label Applicators
Manual applicators are suitable for low-volume labeling tasks. They provide operators with control but require more time and effort compared to automated solutions.
2. Semi-Automatic Label Applicators
These devices require minimal human interaction and can be adjusted for various label sizes. They provide an excellent balance between speed and cost, making them ideal for small to medium-sized businesses.
3. Fully Automatic Label Applicators
For high-volume production lines, fully automatic machines are the best choice. They are incredibly fast and can be incorporated into existing processes for rapid labeling without sacrificing quality.
Industries Benefiting from Machine Label Applicators
The versatility of machine label applicators makes them invaluable across various industries. Here are some sectors that particularly benefit:
1. Printing Services
In printing, accurate labels are essential. Whether it’s for books, packaging, or promotional materials, machine label applicators ensure high-quality application that meets client specifications.
2. Electronics
For the electronics industry, labeling is critical not just for branding, but for compliance and safety. Automated label applicators ensure that every component is correctly labeled, adhering to regulatory standards.
3. Computers
In computer manufacturing, where numerous components require extensive labeling, the use of machine label applicators is essential. They allow for streamlined assembly processes and precise inventory management.
Choosing the Right Machine Label Applicator
Selecting a machine label applicator involves considering various factors to ensure the best fit for your business needs:
- Label Size and Type: Ensure the machine can handle the labels you use.
- Production Speed: Assess the speed necessary for your production line.
- Integration Capabilities: Consider whether the machine can easily integrate into existing systems.
- Cost: Evaluate the initial investment against potential cost savings.
Best Practices for Operating Machine Label Applicators
To maximize the benefits of your machine label applicator, follow these best practices:
1. Regular Maintenance
Routine maintenance is key to ensuring your label applicator runs smoothly. Regular cleaning and hardware checks can prevent costly downtime.
2. Train Your Staff
Ensure that operators are well-trained in using the machine. Proper training minimizes errors and extends the lifespan of the equipment.
3. Monitor Label Quality
Periodically check the quality of the labels being applied. This can prevent larger issues from arising and ensure compliance with industry standards.
Conclusion
The introduction of a machine label applicator can revolutionize your business operations, providing efficiency, accuracy, and ultimately, increased profitability. Whether you’re in printing services, electronics, or computer manufacturing, the advantages of investing in automated labeling solutions are clear. As the market continues to evolve, staying ahead with advanced technologies will keep your business competitive. Explore options that fit your specific needs, and see just how much smoother your operations can run.