The Critical Role of Downhole Filters in the Oil and Gas Industry
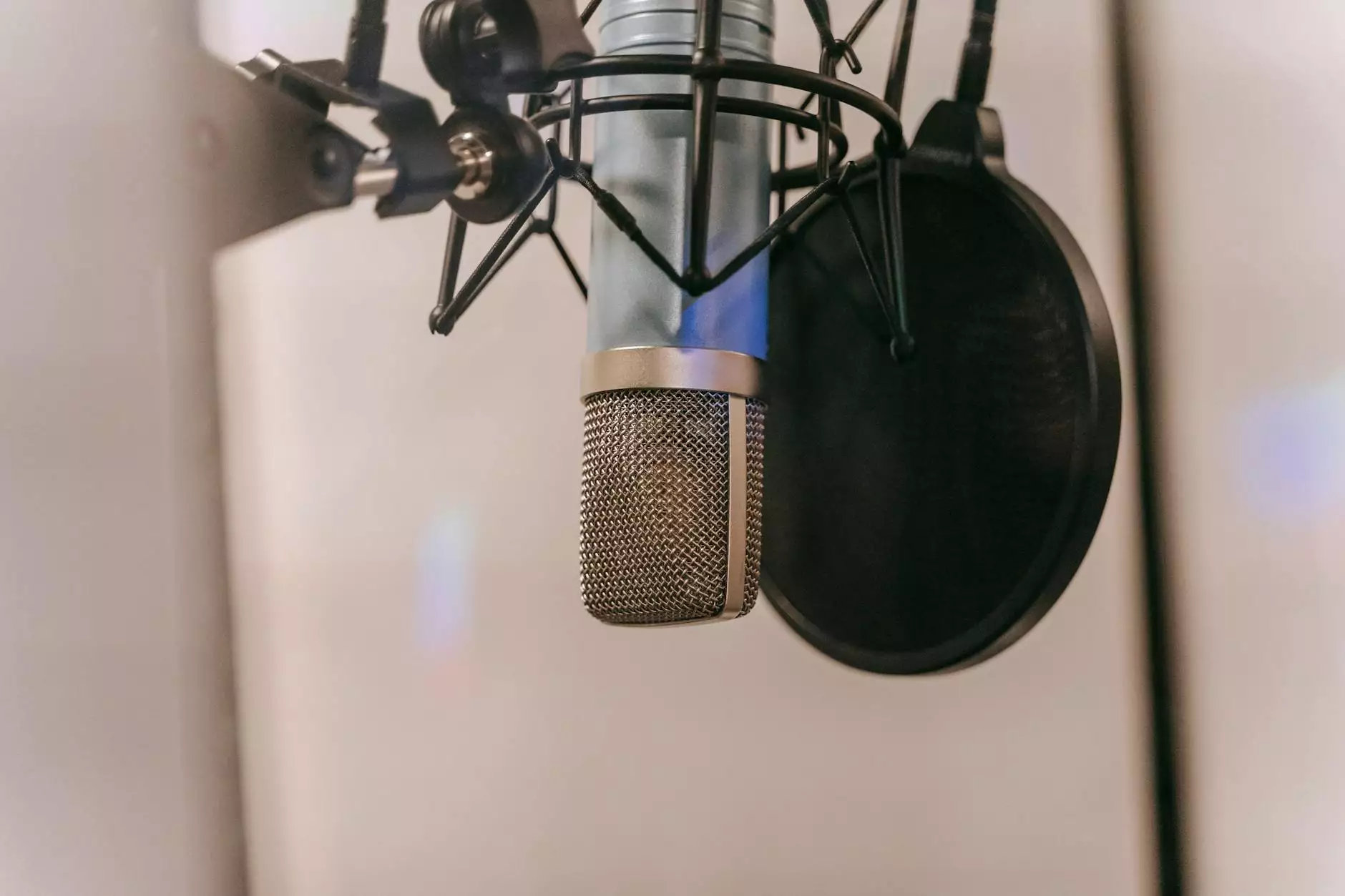
In the dynamic world of oil and gas exploration, the efficiency and effectiveness of drilling operations depend heavily on the quality of tools and equipment used. Among these essential instruments, downhole filters play a crucial role in ensuring the success of drilling operations. Understanding their functionality, benefits, and application can significantly enhance operational productivity and safety.
What are Downhole Filters?
Downhole filters are specialized devices designed to remove particulates and contaminants from the drilling fluid as it circulates through the wellbore. Their primary purpose is to maintain the quality of the drilling fluid, thereby protecting sensitive downhole equipment and improving overall drilling efficiency.
Key Components of Downhole Filters
Downhole filters come with various components that contribute to their functionality:
- Filter Media: The material used to capture solids, ensuring only clean fluid passes through.
- Housing: Encloses the filter media and is designed to withstand high pressure and temperature.
- End Caps: Secure the assembly and help facilitate connection to the drilling system.
Why Are Downhole Filters Important?
The significance of downhole filters in drilling operations cannot be overstated. Here are a few compelling reasons:
1. Protection of Downhole Equipment
Drilling involves the circulation of drilling fluids that can carry various particles. These particles, if not filtered, can lead to wear and tear on pumps, motors, and other essential machines. By using downhole filters, companies can significantly reduce the risk of equipment damage and prolong the lifespan of costly machinery.
2. Enhanced Drilling Efficiency
When drilling fluid is contaminated with solid particles, it becomes less effective in cooling and lubricating the drill bit, which can slow down drilling progress. Downhole filters ensure that the fluid remains clean and effective, thereby maintaining optimal drilling speeds and reducing operational costs.
3. Improved Safety Measures
Contaminated drilling fluid can lead to dangerous situations, including blowouts or equipment failures. Implementing downhole filters can minimize these risks, making drilling operations safer for personnel and reducing liabilities for companies.
The Different Types of Downhole Filters
Downhole filters come in various types, each suited for different applications and operating conditions. Here are some of the most common types:
1. Sand Filters
These filters are designed to capture large sand particles that can cause significant issues in drilling equipment.
2. Mesh Filters
Utilizing a mesh material, these filters can trap smaller particulates, making them ideal for more sensitive applications.
3. Cartridge Filters
Cartridge filters offer a modular approach, allowing for easy replacement and maintenance without significant downtime.
Applications of Downhole Filters
Downhole filters find their application in various aspects of drilling, including:
- Oil and Gas Well Drilling: Essential for both onshore and offshore drilling operations to keep the drilling fluid free from contaminants.
- Geothermal Energy: Used in geothermal drilling to prevent the introduction of solid particles into the system, maintaining efficiency.
- Water Well Drilling: Filters help in maintaining the quality of water being drilled, ensuring clean water extraction.
How to Select the Right Downhole Filter
Choosing the right downhole filter involves considering various factors:
- Particle Size and Type: Identify the primary contaminants present and select a filter that effectively captures these particles.
- Flow Rate: Ensure that the filter can handle the required flow rate without causing significant pressure drops.
- Material Compatibility: Check that the filter material is compatible with the drilling fluid being used.
Maintenance of Downhole Filters
Proper maintenance is crucial to ensure the longevity and efficiency of downhole filters:
- Regular Inspections: Periodically check the filters for signs of wear or clogging.
- Timely Replacements: Replace filters as recommended by the manufacturer to prevent failed operations.
- Cleaning Procedures: Implement cleaning procedures based on the type of filter to enhance performance and extend lifespan.
Future Trends in Downhole Filter Technology
As the oil and gas industry continues to evolve, so too does the technology associated with downhole filters. The following trends are shaping the future:
1. Advanced Materials
Innovations in materials science are leading to the development of stronger, lighter, and more durable filter materials. These advancements can enhance filtration performance while reducing operational costs.
2. Smart Filters
Integration of IoT technology with downhole filters can enable real-time monitoring of filter conditions. This innovation allows for predictive maintenance and reduced downtime in drilling operations.
3. Environmentally Friendly Solutions
With increasing emphasis on sustainable practices, the development of environmentally friendly filter solutions is becoming essential in the industry.
Conclusion
In conclusion, downhole filters are indispensable components of successful drilling operations in the oil and gas sector. Their ability to enhance equipment longevity, improve drilling efficiency, and ensure safety makes them a critical investment for drilling companies. By understanding the types, applications, and maintenance of downhole filters, businesses can optimize their drilling operations and stay ahead in this competitive industry. At Maverick Drilling, we provide high-quality downhole filters and other essential supplies that can help advance your drilling operations. Explore our offerings and see how we can support your business needs.